Fabric Cutting Module
Simplify your Cutting Operations with our customized module
The cutting department's role is pivotal in maintaining quality and efficiency in production, as it sets the stage for the subsequent stages of garment manufacturing. Proper planning, organization, and quality control are essential for a successful cutting department.
Components of our Cutting Module with complete work flow:
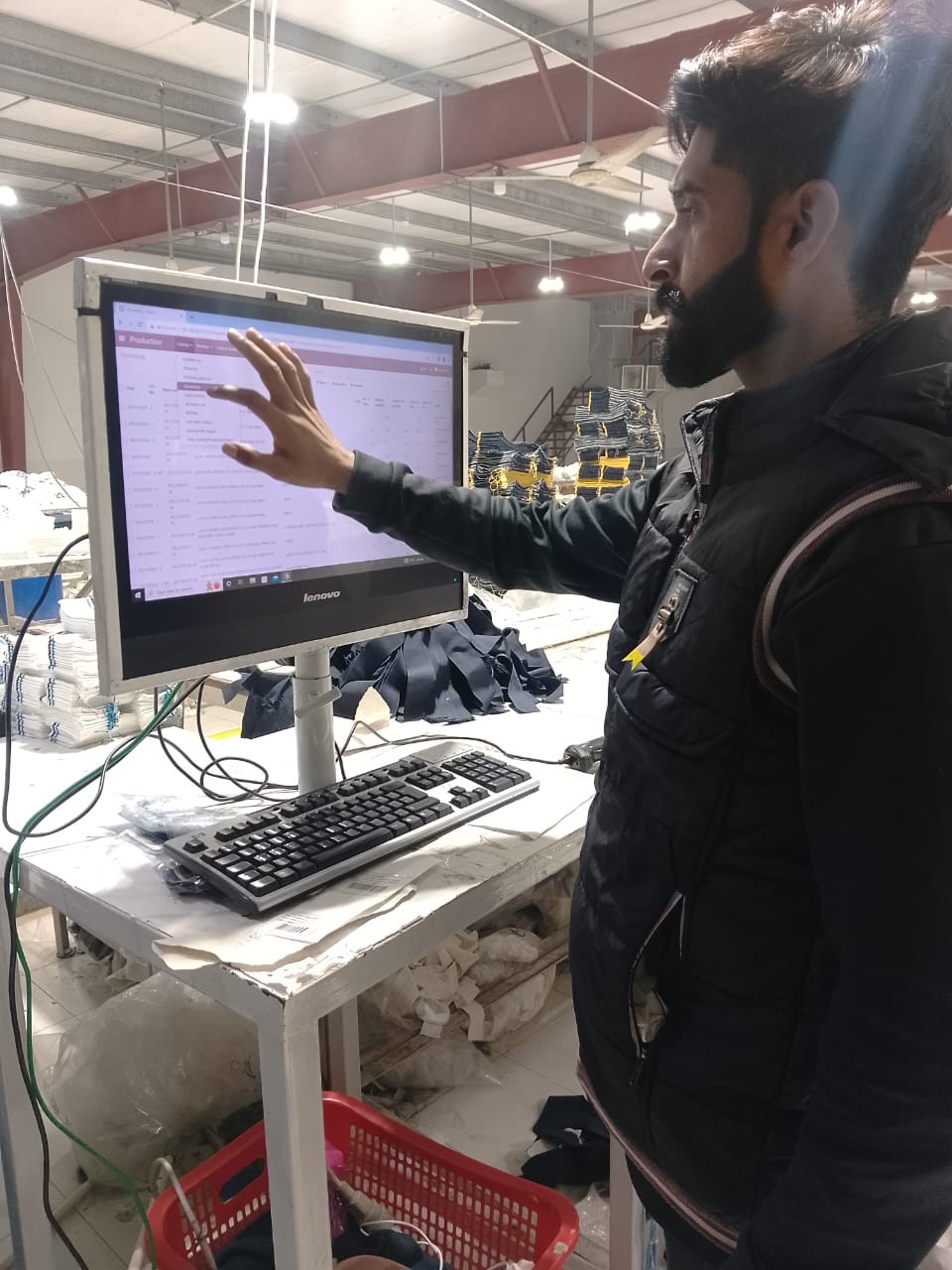
Work Order Receipt:
The process begins with the receipt of work orders from the planning or production department. These work orders specify the type of garments to be produced, the fabric to be used, and the required quantities in different sizes.
Fabric Roll Inspection:
The incoming fabric rolls are inspected for quality and defects by the quality control team. Rolls with defects may be rejected or sent for reprocess if needed.
Fabric Roll Sorting:
Rolls that pass the inspection are sorted based on factors such as colour, fabric type, width and GSM.
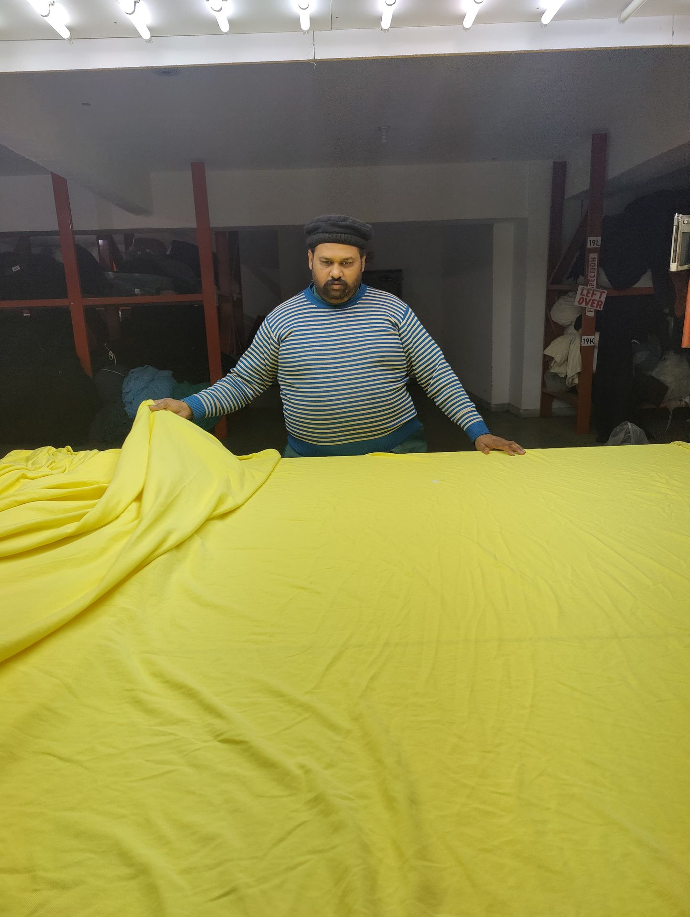
Marker Creation:
The marker is a template that outlines the pattern pieces for each garment size on the fabric. It maximizes fabric utilization and minimizes waste.
The GGT (Gerber Garment Technology) department creates combo-wise markers on the system for each combo of work order.
Markers are defined with the following information:
- Marker ratio for each garment size.
- Number of plies required for that marker.
- Required number of pieces for each size.
- Planned cuttable quantity for each size.
- Estimated waste in kilograms.
- Estimated fabric consumption.
- Marker efficiency as per fabric GSM.
Pattern pieces are placed on the marker, and the layout is adjusted to achieve the most efficient use of fabric.
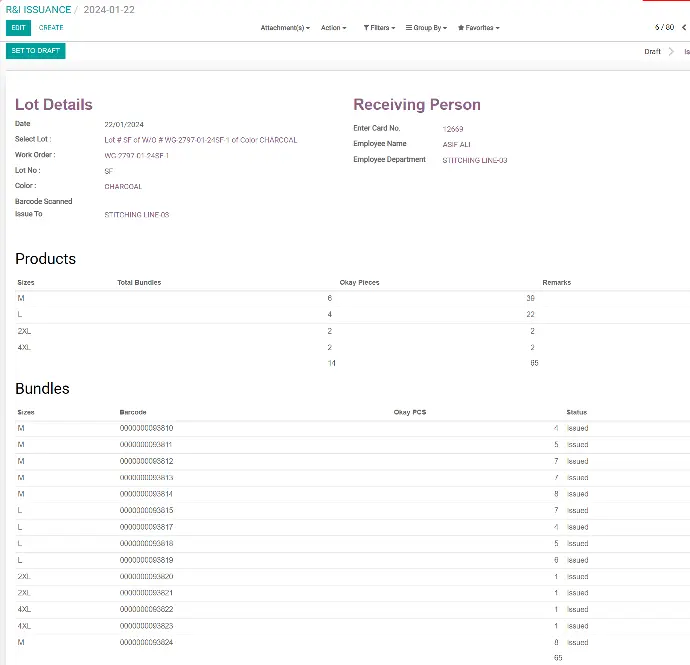
Fabric Spreading:
The fabric spreading process involves laying out the fabric in layers according to the marker template .Automated fabric spreading machines are often used for this purpose. The goal is to create a stack of fabric layers that matches the marker's specifications.
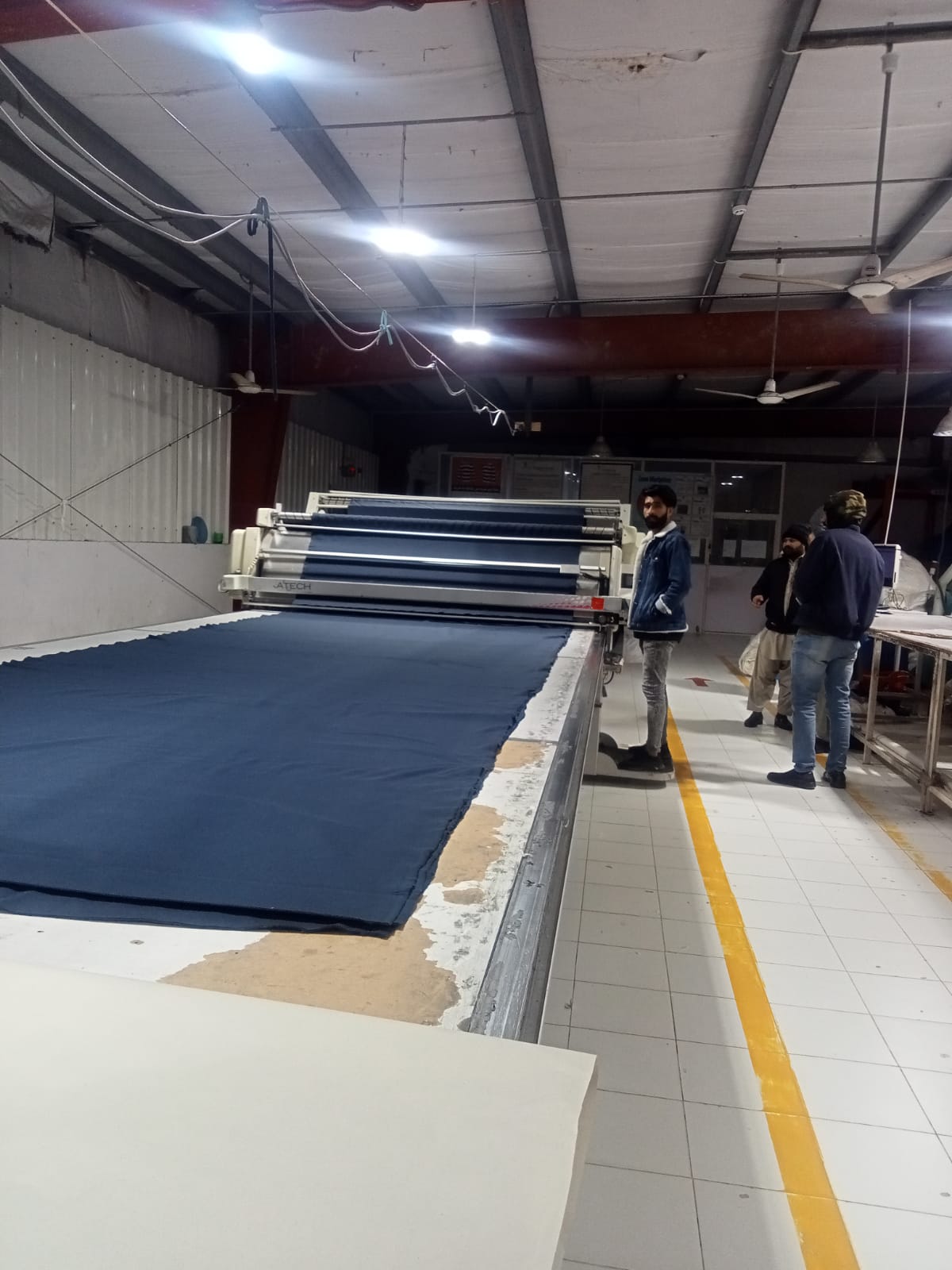
Pattern Cutting:
The actual cutting of fabric into pattern pieces is performed by skilled operators using cutting machines such as straight knife, rotary, or laser cutters.
Operators follow the marker's outlines to cut the fabric accurately. They open the markers on their system and scan fabric rolls and then they enter actual plies for each fabric roll scanned. As per actual number of plies and marker ratio for each size, system auto calculates the actual cut quantity for each size and balance quantities to be planned/cut for the same work order in the next marker.
System generates Work order wise cutting reports which provides comprehensive detail of actual cut quantities, comparison between planned consumptions and actual consumption, planned wastages and actual wastages
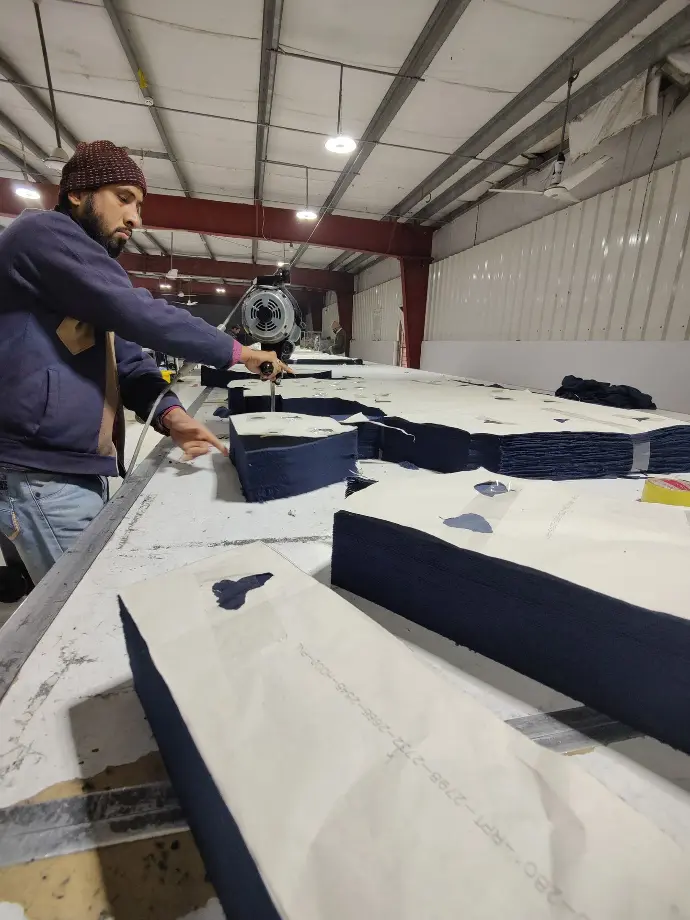
Panel Bundling:
Once all pattern pieces are cut and inspected, they are bundled according to garment size. As per marker detail, system auto generates barcode labels containing relevant information for each bundle and bundle report for each marker.
Bundle per piece is also adjustable in settings.
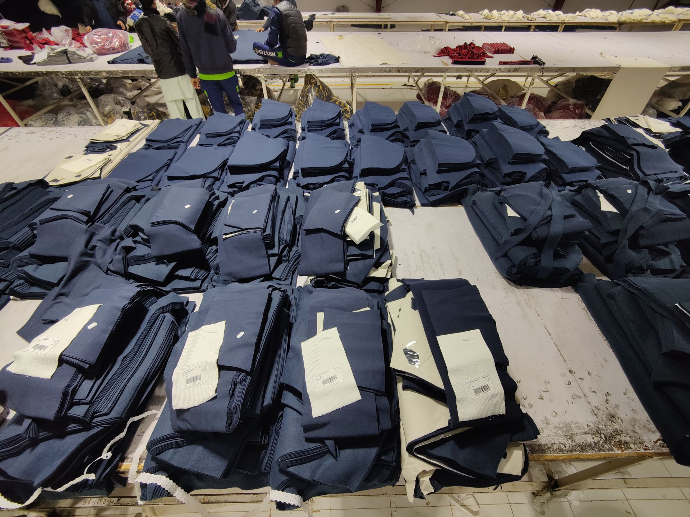
Quality Inspection:
After cutting, quality inspectors examine each cut piece for defects, accuracy, and adherence to size specifications. Quality inspectors use tablets for this purpose. They have a pre-set button for each fault category which they enter by simply clicking on it. As per entered faults, system auto generates Quality inspection reports.
Any flawed pieces are separated for rework or replacement. After complete inspection the bundles are then presented for audit.
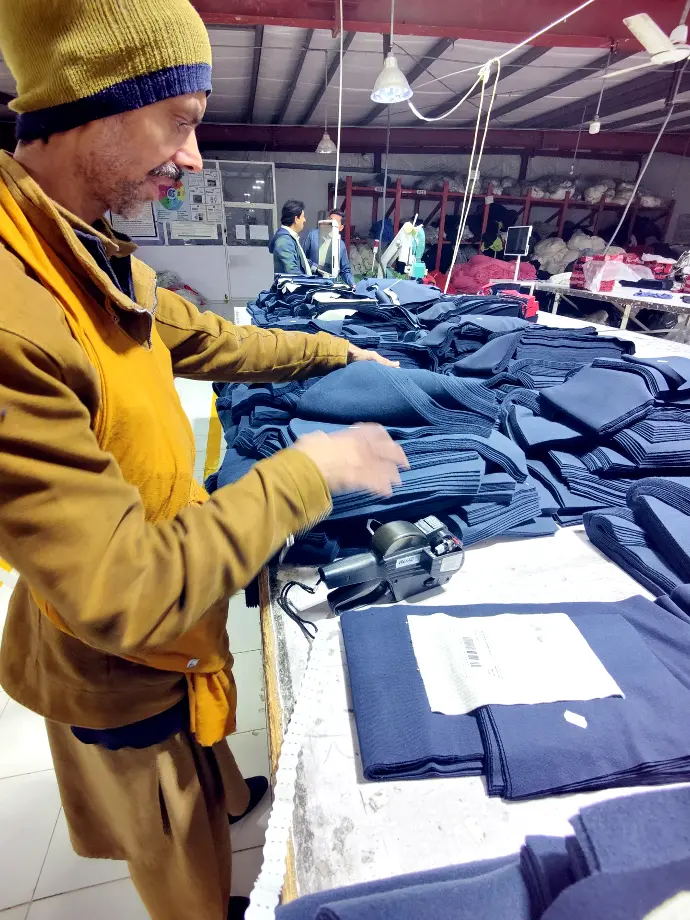
Quality Audit:
A final quality audit may be conducted to ensure that all bundles meet quality standards. An independent auditor checks the bundles for accuracy and consistency.
The auditor has his own separate menu which he uses to enter his own findings. He randomly selects bundles and compares his findings with Cutting Quality inspectors reports.
If he is satisfied with quality then he approves all bundles for induction by simply clicking on the Approve button. And without his approval, no bundle can be inducted which is very important to maintain quality standards and avoid rejections from the third party audits.
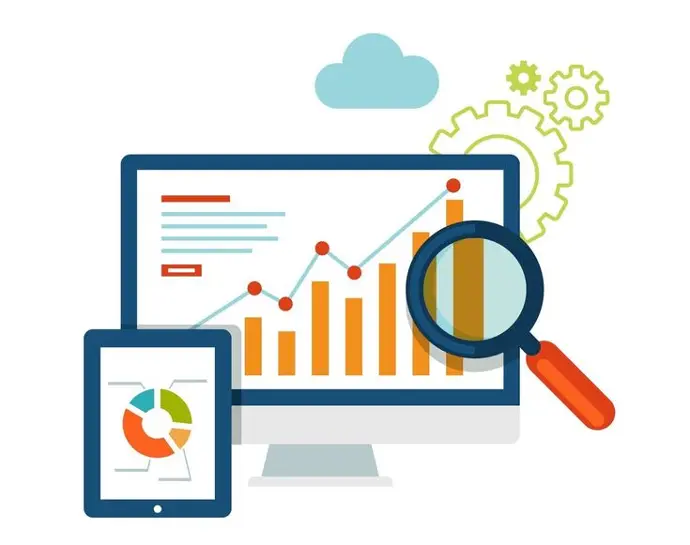
Inventory Management:
- The cut pieces are recorded in the inventory system to keep track of the quantity of pieces for each size and style.
- Inventory management ensures that the correct number of pieces is available for stitching.
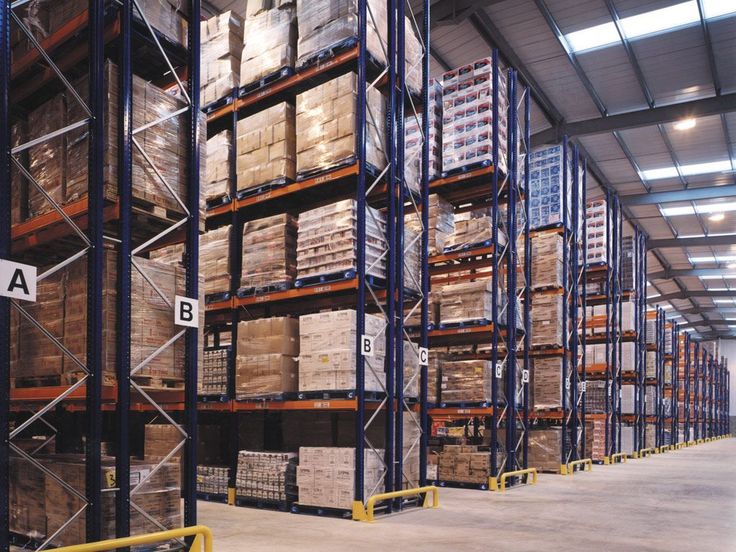
Bundle Issuance:
- Bundles are issued to the stitching department based on production schedules.
- The bundles are accompanied by documentation specifying the style, size, and quantity to be sewn.
- This is done by creating a simple form for each work order. After that the system operator uses a barcode scanner to scan barcode labels pasted on each bundle.
- By doing this way, bundle quantities can not be changed manually and helps in promoting transparency and safeguards from theft.
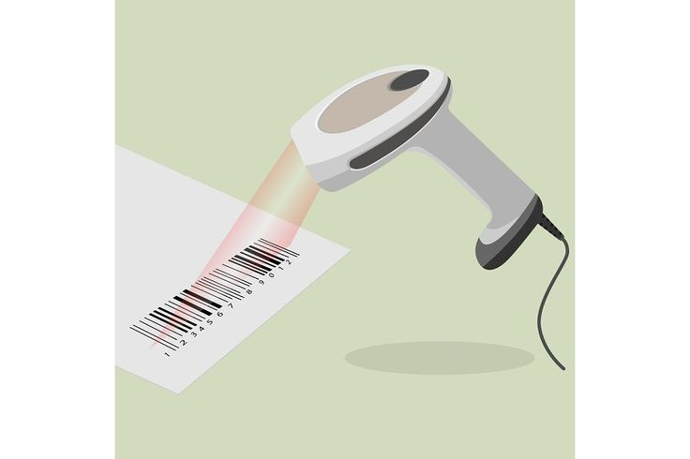
Reporting:
Following reports are generated in cutting module:
- Daily Cutting Production Report.
- Work Order Wise Cutting Report.
- Cutting Planning Report.
- Bundle Report.
- Cutting Quality Inspection Report.
- Internal Audit Report.
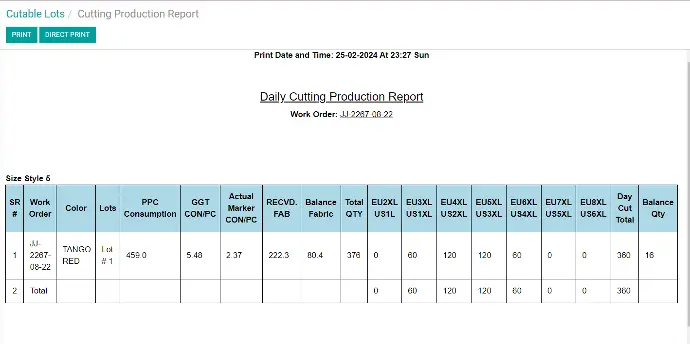
Benefits of Using Our Fabric Cutting Module
Enhanced Efficiency:
The Fabric Cutting Module streamlines the entire fabric cutting process, from marker creation to bundle issuance, optimizing each step for maximum productivity and reducing manual errors.
Improved Accuracy:
By utilizing automated systems for marker creation and fabric spreading, the module ensures precise cutting of fabric pieces, minimizing fabric wastage and enhancing overall accuracy in garment production.
Real-time Monitoring:
With comprehensive reports generated at each stage, including cutting production, work order-wise cutting, and quality inspection, users gain real-time visibility into the cutting process, enabling proactive decision-making and troubleshooting.
Quality Control:
The module incorporates quality inspection functionalities, allowing inspectors to examine each cut piece for defects and ensure adherence to size specifications, thereby maintaining high-quality standards throughout production.
Inventory Optimization:
Through integrated inventory management features, the module accurately records and tracks the quantity of cut pieces for each size and style, facilitating efficient inventory management and ensuring the availability of the correct number of pieces for stitching.
Transparency and Accountability:
The use of barcode labels and automated bundle issuance processes promote transparency and accountability in the cutting process, reducing the risk of manual errors and promoting a culture of integrity and trust within the organization.