FABRIC ROLLS TRACKING SYSTEM
Roll Tracking Software offers textile companies a powerful tool for optimizing their production processes, ensuring quality, and enhancing efficiency at every stage of production. It provides valuable insights and analytics to support informed decision-making and ultimately helps textile manufacturers deliver high-quality products to their customers.
Key Components of our Roll Tracking System & Work Flow
Rolls Reception in Greige Store Department:
- Fabric rolls, after being woven, are received by the Greige Store Department.
- Greige Store inspectors perform initial inspections on these rolls.
Fault Identification and Entry:
- During the inspection, quality inspectors identify fabric faults.
- The software provides a user-friendly interface with a list of available fault types.
- Quality inspectors enter identified faults by clicking on corresponding buttons.
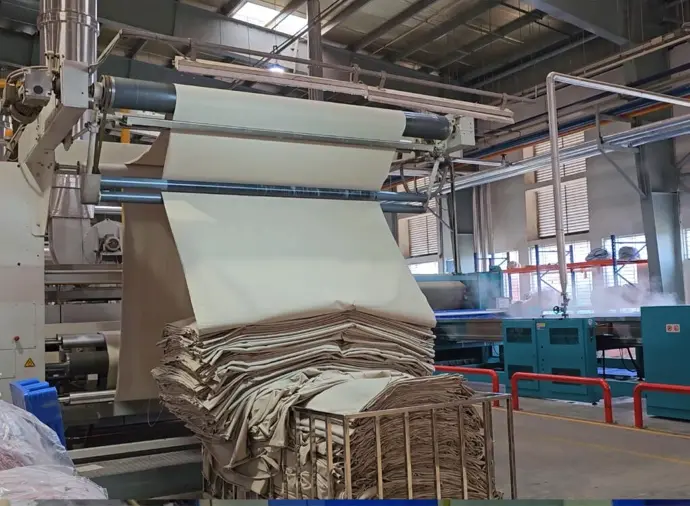
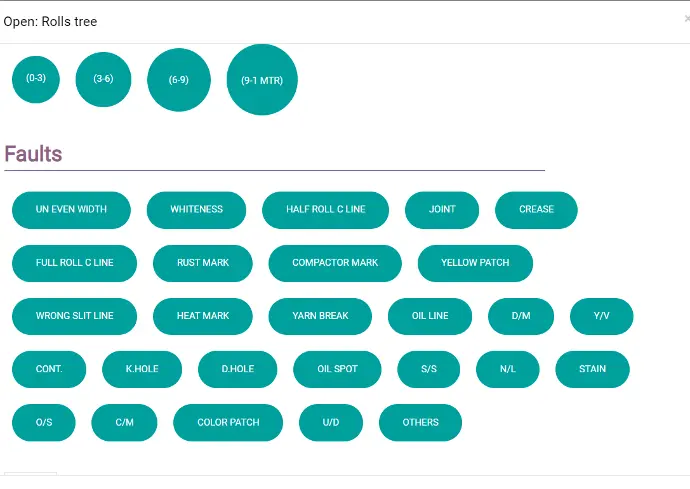
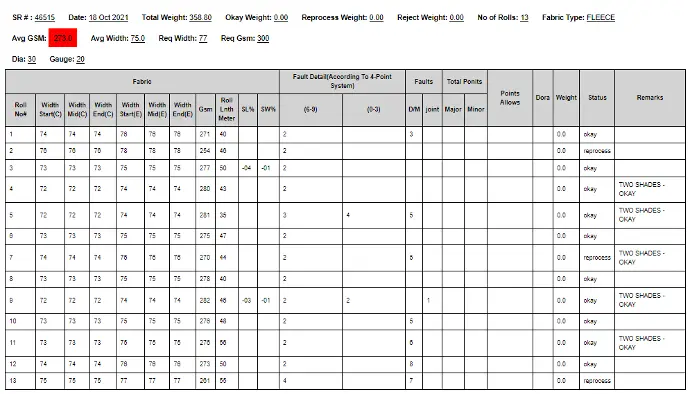
Inspection Report Generation:
- The software compiles the inspection findings for each fabric roll.
- It categorizes rolls into A, B, or C categories based on the identified faults.
- As the inspection progresses, the system records fault findings in real-time.
- An inspection report is automatically generated, detailing the faults found in each roll and its category.
Barcode Label Printing:
-
The Greige Store Department generates barcode labels and attaches the printed barcode labels to their respective fabric rolls.
-
These barcode labels are specifically designed to withstand the heat of the dyeing process.
-
The German-made barcode printer recommended by us ensures label durability.
- These labels remain readable even after exposure to the heat of the dyeing machine.
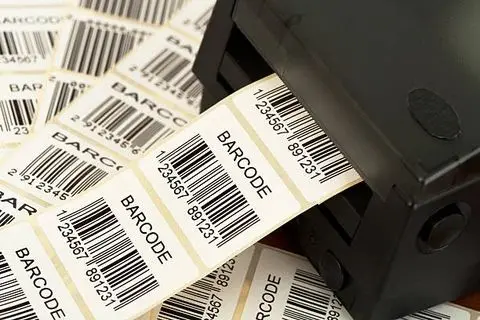
Fabric Rolls Issuance
- After Quality inspection, Production department creates a Fabric Lot on system and as per the lot specifications, Greige store department issues Fabric rolls to dyeing department for processing.
- After fabric rolls are dyed, these rolls are transferred from the dyeing department to the Finishing department.
- Finishing department again generates faults finding reports after the dyeing process.
- After fabric rolls are dried and the Finishing department has completed its job, rolls are then moved from Finishing to Stitching department.
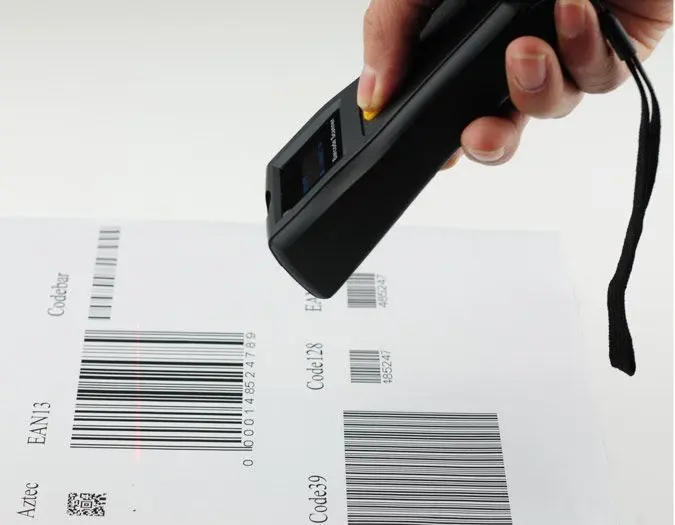
Roll Tracking and Status Reports:
- Our software provides multiple reports to facilitate roll tracking and monitoring.
- The Roll Tracking Report provides a detailed overview of the rolls' movements and status.
- Customers can easily track the status of each roll within various departments, including Greige Store, Dyeing, Finishing, and Stitching.
- The Roll tracking report also provides complete detail to our customers like how many rolls for each work order and for each size were weaved? How many rolls were received by the Greige store department, Dyeing, Finishing and Stitching department?
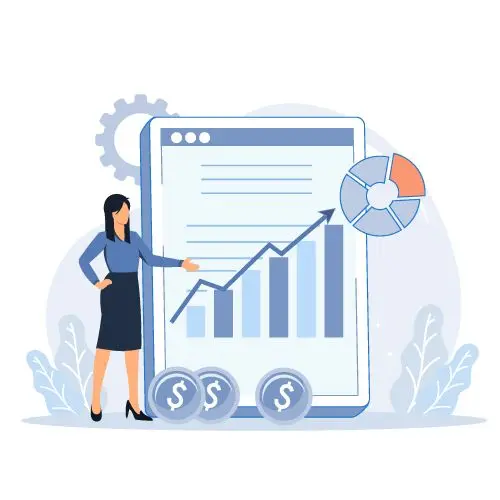
Work Order Analytics:
The main report offers a comprehensive analysis of work orders:
- It shows the required quantity for each size in the work order.
- It tracks how much fabric has been woven and how much is still pending.
- Shows how many pieces were extra weaved.
- Shows how many pieces of B Category were weaved.
- Shows deviation of B category of pieces from Company’s pre-set tolerance percentage.
- It monitors the progress in the dyeing, finishing and in the stitching department.
- Users can easily track the progress of each work order and determine which ones are complete and ready for shipment.
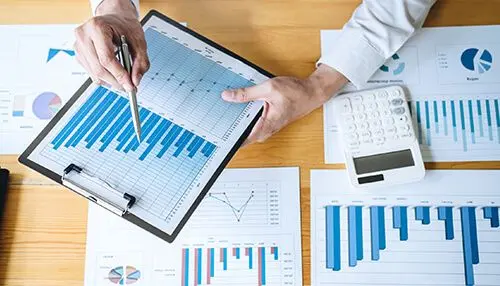
Benefits of Using Our Roll Tracking Software
Enhanced Quality Control:
The Roll Tracking Module enables comprehensive fault identification and entry, facilitating meticulous quality inspections at various stages of the fabric production process. By categorizing rolls based on identified faults, it ensures that only high-quality fabric is processed further, minimizing defects in finished products.
Improved Transparency and Accountability:
Customers gain access to detailed quality inspection reports, providing transparency into the condition of fabric rolls at each stage of production. With the ability to track roll movements and status in real-time, stakeholders can monitor progress, identify bottlenecks, and hold departments accountable for their responsibilities.
Streamlined Workflow:
The module optimizes the fabric production workflow by automating processes such as barcode label printing and roll issuance. This streamlines operations, reduces manual errors, and enhances overall efficiency in managing fabric inventory and production schedules.
Data-Driven Decision Making:
Through comprehensive analytics and reporting functionalities, the module offers valuable insights into work order progress, fabric utilization, fault trends, and adherence to quality standards. These analytics empower users to make informed decisions, optimize resource allocation, and improve production efficiency.
Improved Customer Satisfaction:
By providing customers with visibility into the quality and status of their fabric orders, the Roll Tracking Module enhances communication and trust between textile manufacturers and their clients. Customers can make informed decisions based on real-time data, leading to higher satisfaction levels and strengthened business relationships.
Compliance and Audit Readiness:
The module ensures compliance with industry regulations and quality standards by maintaining detailed records of fabric roll movements, quality inspections, and production metrics. This enables textile companies to demonstrate regulatory compliance during audits and inspections, mitigating risks and enhancing credibility in the market.
Our Roll Tracking Module is the cornerstone of efficient workforce management with transparency. It provides a holistic solution to address production challenges, improve employee efficiency, and ensure accuracy.
Contact us today to learn how our Roll Tracking Module can transform your operations, regardless of the size or complexity of your organization.